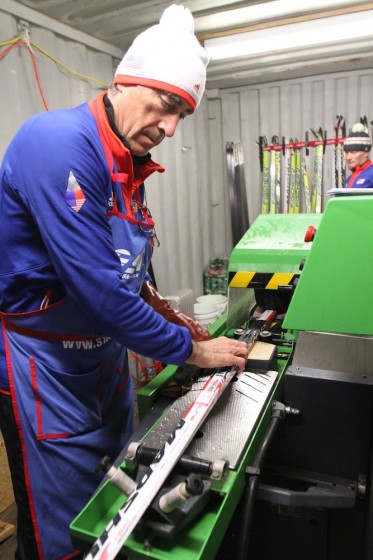
FasterSkier’s coverage is made possible through the generous support of Rudy Project.
SOCHI, Russia – Ski preparation—the strange pseudo-science of applying waxes and structures to the bottom of skis to make them go faster—is such an important component of racing that the powerhouses of cross-country skiing and biathlon, like Norway and Russia, have entire semi trucks at the Sochi Olympic Games housing their workspaces and equipment.
Then, there’s the U.S. biathlon team, which operates here out of a ramshackle orange shipping container cluttered with machinery and coiled extension cords—with a couple of full beer cans propping up their jury-rigged waxing bench.
Inside the container, the American team staff uses a $125,000 machine to grind skis for the Olympic cross-country and biathlon races—running the skis along a rapidly-spinning cylindrical stone that applies a pattern to their plastic bases.
The patterns are tailored to specific snow conditions, and the Americans have adjusted them for different events here, as the weather has changed and the thermometer has spiked—in theory helping to give their athletes an edge over the competition.
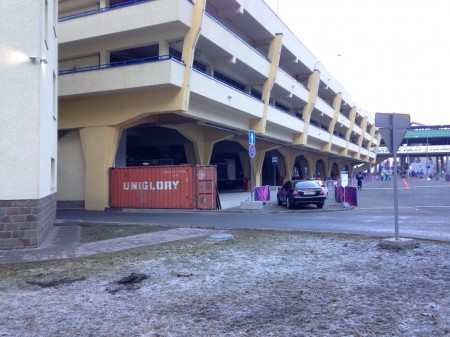
After placing eighth in the men’s individual race earlier this week, U.S. biathlete Lowell Bailey said that the speed of his skis was a “huge advantage.”
“And that’s due to a few people that have been working specifically for these races,” he said, alluding to the biathlon team’s ski technicians.
A day before that race, Bailey’s skis had been propped up along the wall of the container, with a dozen more pairs belonging to his teammates, and to American cross-country skiers.
Inside, three members of the U.S. biathlon team’s staff were working with the stone grinding machine, churning out skis that would be used in races over the next several days.
The cramped container pales in comparison to the Norwegian and Russian trucks stationed nearby. But it works, as evidenced by Bailey’s eighth-place finish.
“Looks more fancy,” said Bernd Eisenbichler, the high-performance director for the U.S. biathlon team, motioning at the other country’s trailers. “But the outcome, I think, is better here.”
Over the whine of the equipment—which in addition to the grinder includes a pair of heaters, an air compressor, and a generator—Eisenbichler, a German who’s worked for the U.S. since 1999, explained how the team had arranged its Sochi setup.
The container, to which the Americans have added a plywood wall and a door, had been set up in U.S. and shipped to Europe for about $15,000. It cost nearly as much again to rent the space where the container sits in Sochi, below a gondola that runs up to the competition venues, Eisenbichler said.
The money for the initial testing came from the biathlon and cross-country ski teams, which are both using the grinds, while the cost of shipping the container and renting the space was defrayed by the U.S. Olympic Committee.
“They understand the importance of fast skis to be competitive,” Eisenbichler said of the USOC.
As the high-performance director for the biathlon team, the Sochi ski service project falls under Eisenbichler’s responsibility.
But the key to the whole thing is Muck Bauer, the tall, avuncular German who runs the grinding machine.
A 59-year-old former alpine ski racer who hails from Bavaria, Bauer worked for the Germans for five years before being hired by the
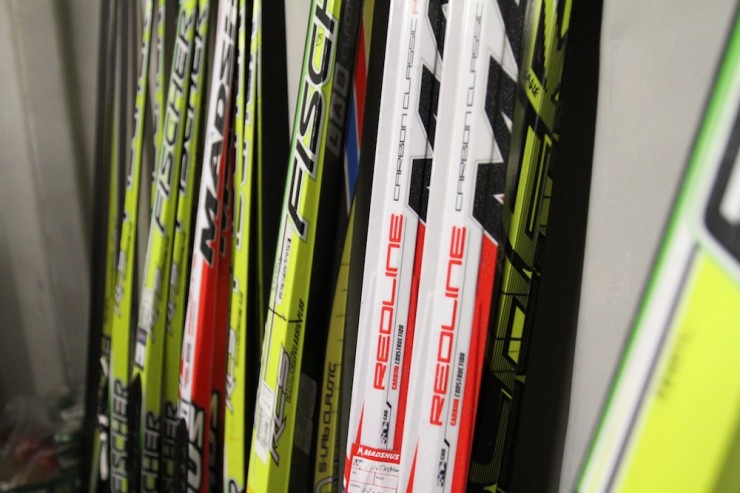
Americans; he’s now under an exclusive contract that bars him from working with any other teams.
He’s charged with operating the grinder—calibrating, among other things, the thickness of the grinds, the angles, the pressure and speed at which they’re applied. The different settings affect how the skis slide on different types of snow crystals; deeper grinds are used for wetter snow because they can help reduce suction, which would otherwise slow athletes down.
Bauer owns a sports store in Germany, and got his start in the field because, as he put it, he was interested in making his own skis, and his friends’, go faster.
“I want to have good skis under my feet,” he said, with Eisenbichler translating from German.
Under Bauer’s agreement with the Americans, the grinding parameters belong to the U.S. team, but he is allowed to use some of them in his store in Germany, selling the patterns to recreational athletes.
Bauer keeps a book that holds the numbers he plugs into the machine, and they’re also stored on a hard drive. The information is closely guarded: It’s never sent over email, Eisenbichler said, and it’s never left in the container.
“We take all the data with us every day,” he said.
The process of finding the best grinds is not scientific, said Zach Caldwell, who developed patterns for the American cross-country skis leading into the last Olympics, in Vancouver in 2010.
Mostly, it entails testing skis over and over again after they’ve been run through the machine on different settings, he said.
“There’s not a very good way to apply science to it, so you’ve just got to put stuff on the snow and see what works,” he said.
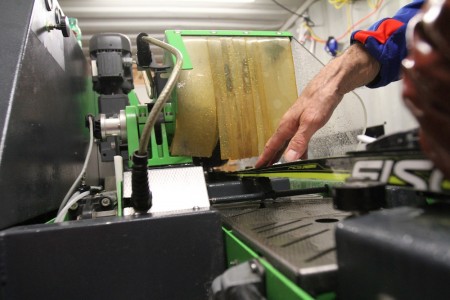
Before the Sochi games, the U.S. team tested grinds at three different events here—a string of biathlon, cross-country, and para-nordic races that took place a year ago.
They started with 120 different options, Eisenbichler said, which had been narrowed down to about two dozen when the team’s staff arrived in Sochi a few weeks ago.
By the time the games started, the U.S. had settled on just three grinds: one for dry, newer snow, one for warm, wetter snow, and one for conditions that are somewhere in between.
“You work with a lot of skis at the beginning, then narrow them down,” Eisenbichler said.
On Wednesday, the Americans fired up the grinder at 9 a.m., sent a couple dozen pairs of skis through, and were back up at the venue a few hours later.
The next day, Bailey would be using a pair to race to his historic result in the individual race—the payoff for the many hours of work spent inside the container, and on the testing over the last year.
As to whether the beer cans propping up the wax bench were still full, Eisenbichler responded: “There are two different ones there now.”

Nathaniel Herz
Nat Herz is an Alaska-based journalist who moonlights for FasterSkier as an occasional reporter and podcast host. He was FasterSkier's full-time reporter in 2010 and 2011.