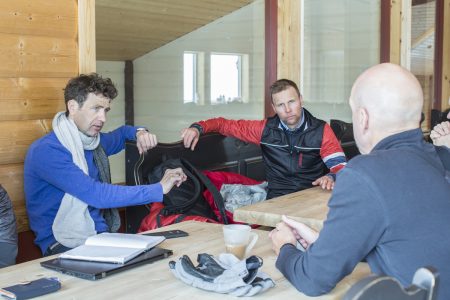
We don’t often worry, or even think much, about the layers of ownership involved in the ski industry. But last October, Newell Brands announced that it would be selling off its winter sports holdings following a merger with Jarden, the parent company of K2, and subsequently Madshus. Newell and Jarden are big players in in the consumer products world, accounting for common brands like Rubbermaid, Coleman, and Mr Coffee, to drop a few recognizable names from a long list of other recognizable names. The winter sports market is small potatoes in the world of Rubbermaid and Coleman, and it’s not a surprise that Newell Brands decided not to pursue the winter sports industry, which is notoriously difficult and unstable business.
When they announced the sale, Newell also announced that they wanted to move fast, and would consider shutting down assets that did not sell quickly. In addition to Madshus the K2 holdings included Volkl, Marker, Dalbello, Line, Atlas, Tubbs, and others. The whole package was being sold as a bundle, and the big question was whether a buyer would keep the package intact, or immediately split everything up – keep some brands, sell others, and close the duds. The concern for Madshus dealers in the US was that K2 is not only the parent company; it’s also the distributor in the US market. A break-up could have meant a change in distribution, which could have been very disruptive to the supply chain and customer support in the US.
The Corporate acquisition story turned out happily. Kohlberg & Company – a private equity firm with at least one consultant on the team who is seriously invested in Nordic skiing – bought K2, and left the structure intact. That means that business with Madshus is business as usual.
If some of us American retailers were getting a bit jittery over the ownership situation this last winter, the folks at Madshus in Biri never seemed to lose any sleep over it. Madshus hasn’t always been a tight ship, but in recent years they’ve been stable, well organized, and independently profitable. No matter what ownership shake-up went down, Madshus was always going to land on its feet.
And if some people in the industry were taking a “wait and see” approach, the Madshus race and development program was full speed ahead. In the spring of 2016 Per Wiik told me that he had secured the funding to add a full time position to the race development program, and by fall of 2016 Madshus had hired Svein Ivar Moen away from the Norwegian Biathlon team. Svein Ivar had worked directly with Ole Einar Bjorndalen as a tester and waxer for years, and was already deeply involved with the Madshus brand.
So, at about the same time that Newell Brands was announcing that K2 would be sold, Madshus was starting an entirely new development project. Svein Ivar’s job was to coordinate testing and manage the huge amount of information that would be generated by a development and testing process in which almost every variable in the ski construction process was open for revision.
When we say things like “every variable is open for revision” it’s necessary to clarify a point or two. Every ski brand has developed a method of building skis using a certain set of materials and manufacturing processes. It’s common to see similar materials – sometimes from the same supplier – in skis from different brands. But the construction method is unique for each brand, and it represents a massive investment in factory tooling and process development. What Madshus did not set out to revisit in the last year was their construction method. They didn’t proposed to redesign the structure of the skis from the inside out.
What they did open up for assessment is everything else. The geometric shape of the skis, including the sidecut, the thickness profile, and the 3-D shape, all contribute to the stiffness profile and the performance characteristics of the skis. A ski of a different shape is a fundamentally different object, and will behave differently. And once the physical dimensions of the ski are defined, there are a huge number of different camber variations and ideas that can be explored. Because of their materials and production methods, Madshus can manipulate and control cambers with a level of precision and flexibility that is unmatched in the industry. If Madshus has any advantage over other brands, it’s the degree to which they can manipulate and reproduce cambers.
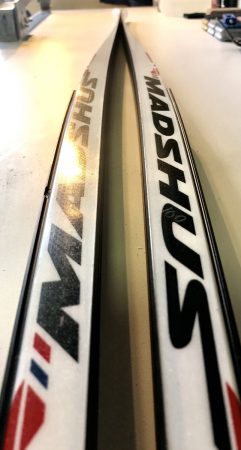
Camber is often a misunderstood factor in ski construction. Unlike bikes, or ski poles, or most other sports equipment, skis are dynamic objects – designed to bend. The materials and physical shape of the skis define the physical characteristics of the object. But those physical characteristics only matter when the ski is in motion over varying terrain, under ever changing loads. The camber is what determines the expression of the materials – how they behave between the skier and the snow. Camber is where the variation from one pair of skis to the next occurs, and it’s what we travel to Norway to select.
When you think about the number of iterations possible between different sidecuts, different thickness profiles, and different cambers, the possibilities seem almost endless. It was these endless possibilities, and the results that they generate in different types of conditions, that Svein Ivar was brought on board to manage. At the start of the process there was no clear idea how things would come out. How many lengths would there be? How many different models? How many camber variations? Would there be different geometries for different conditions? A year ago, all of these questions were open, and on the table. After meeting Svein Ivar, and discussing the project with him and Per for the first time last September, my head was swimming with the sheer scale of the task ahead.
We visited Norway twice this spring; once in March for a family vacation in Sjusjoen, and once in May to begin selecting skis for the coming season. I don’t know anything about the process that occurred over the bulk of the winter, except that the Madshus team tested a lot of different materials. In March we had an opportunity to try some new skis. The classic skis were a finished product – a subtle but significant change from the previous model, and a joy to ski on. But the skate skis were… well – they were a work in progress. They had excellent edge stability, and good low speed release on icy snow, but they were really unresponsive to active skiing, and had a tendency to lose speed very quickly. Per had warned me that they were unsatisfactory, and my feelings weren’t unique.
We went home from Norway, and didn’t think too much about skiing for a while, until we returned to select skis over eight weeks later in May. When we returned the Madshus team had just wrapped up their final days of an intensive testing program based out of the Natrudstilen stadium in Sjusjoen. They had been testing skis every day since the conclusion of the World Cup season, including a bunch of new model testing with many of their top World Cup athletes.
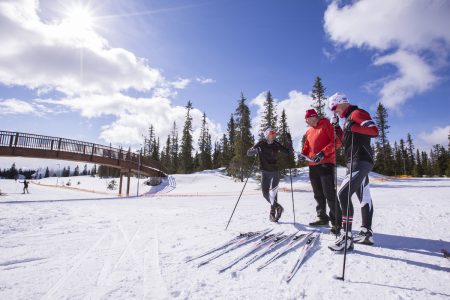
The skate skis had been revised with entirely new molds, and the testing had gone well. The snow was pretty well used up, and the last day of grooming was the day before we arrived. But that didn’t stop Amy and me from getting out on the slushy “crust” up in Sjusjoen every morning that we were there, to “test” the new skis. We also took some of the most race proven skis from the old model for comparison, and we slogged through a season’s worth of accumulated klister residue, dirt, and dog hair. And although we didn’t expect the conditions to provide any real testing, there was no question which skis we liked. The new skis were faster, and easier to control, even when they were totally coated with dog hair.
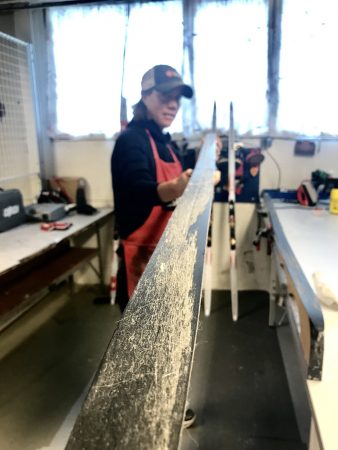
Given our limited experience with the skis, we weren’t surprised to hear that all of the athletes who tested the new skis wanted to race on them. It was an encouraging vote of confidence, even if the team hadn’t yet decided exactly how to configure the models and cambers. I had a very interesting meeting with Per and Svein Ivar, discussing the process, and what they had learned. Svein Ivar showed me a couple of skis from a couple of different productions, and asked me what I thought. Maybe it was a bit of a test, and I don’t know whether I passed or failed, but I do know that I appreciated (and was flattered by) the attention, and the engaging discussion.
So, what now? I’m know that some new models are being produced for World Cup racers, because that’s the next stage in development and testing. It’s the same with us, when we make a new grind. We start by casting a wide net with a new concept, and we do our own testing. If something encouraging emerges after a season of testing, then we start to produce it for use by racers in a controlled setting – where we know that we’ll receive both good and bad feedback, and we’ll gather information from a wide variety of conditions and venues. That second stage of testing is where I consider the real proof to reside. Until a grind is producing good race results in a variety of venues, with a variety of athletes, it hasn’t been proven.
Every time we test Madshus skis in Lillehammer or Sjusjoen, they’re amazing. Sometimes we take along other skis to compare, and it’s usually pretty clear that Madshus has their home environment dialed. It’s not a surprise, since that’s where they do most of their in-house testing. Madshus needs World Cup skiers to get that next stage of testing – a wider variety of testers using the material all over the world. When the skis are reliably producing results on the World Cup, then it becomes the job to figure out how to bring the concept to the market.
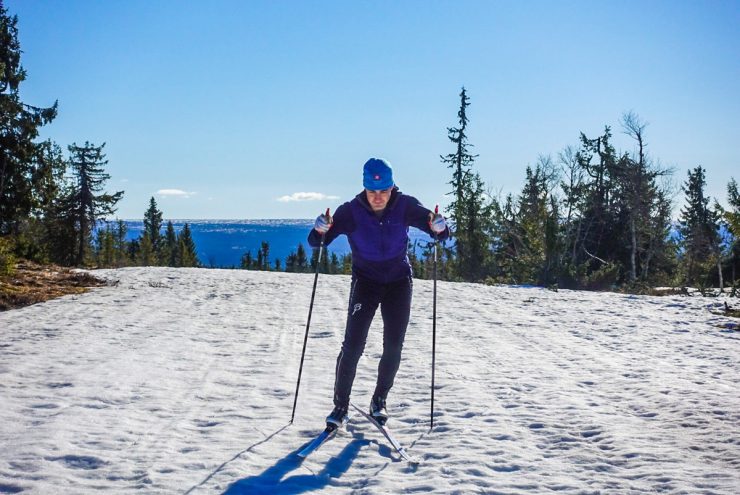
Ski companies survive by selling skis to skiers, and the racing programs exist to support that process. One of the things we like about Madshus is how direct the links are between development and racing and production. I have no idea whether the ski designs that we tested this spring will succeed on the World Cup and make their way to production, though I have a pretty good idea that they’ll do well in competition. It’s inevitable that another round of testing new concepts will follow this one. After all, Svein Ivar is there full time to drive that process along. When they know that the design is good, both in terms of performance and in terms of flexibility, then we’ll see new skis on the market.
While the scope of the testing project hasn’t always been as broad as it was this time around, a similar process has worked to produce incrementally better skis every couple of years for as long as we’ve been paying attention. It’s not so different with other companies – development never ends. Madshus is unique because they’re very open with their process.
I have been obsessed with skis since I was a kid, and I’ve made a living selecting and tuning skis since I was a young(er) adult. If this job were a question of simply taking what we’re given by the ski companies and passing it along to customers without ever trying to understand what went into the skis in the first place, it would be incredibly boring. When Madshus shares their process with us, it feeds our interest and enthusiasm for their work, and we want to share it with you in hopes that it makes you excited as well.
We’ve scheduled our fall ski selection trip to Norway for the first week of October – a month later than normal. That’s to give the factory time to produce some of the new models that we’ll be picking for Brian and Caitlin Gregg, Noah Hoffman, Ida Sargent, and Liz Stephen. Liz will join the Madshus team this winter after some very encouraging testing in Bend in early May. We’ll also be selecting skis for customers and shop inventory on that trip. Get in touch if you’ve got Madshus fantasies that need fulfilling.