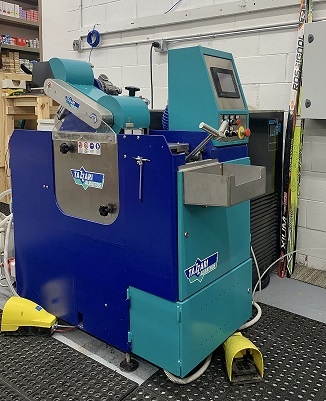
With hand-picked skis arriving and heading out the door to customers, we are prepping a high percentage with a grind on our Tazzari Stonegrinder followed by a Thermo Box and Race Hardening treatment. This may seem like overkill for a brand new product but there are countless reasons why we take the time to grind your brand new skis before they see the snow. Buying a new pair of race skis without grinding them is a little like buying a new bike and not airing up the tires before heading out for a ride; you still have an excellent product fit specifically for you, but you are giving up a key factor in performance. On the World Cup level, skis are frequently ground before every single race and are always ground for the athletes when they are new. You may not be a World Cup racer but why not take advantage of all the speed you can get, especially when you just spent money on a brand new pair of skis?
There are multiple reasons why we grind brand new skis, all with the idea of consistent speed and performance regardless of the conditions. All of our grinds at Pioneer Midwest have hundreds of hours of testing and racing in various conditions and temperatures so you can be sure that you are getting the most out of your ski investment.
The main issue we run into with the factory structure is the lack of post-grind ski service and attention. Skis are cut, formed, and lastly sent through a production line where a factory grind is cut into the base of the ski. These grinds are not inherently bad or slow, however, this stonegrinding machine cuts hundreds to thousands of skis per day with minimal maintenance or cleaning. This in turn leads to variation in grind quality and clarity which we have witnessed firsthand no matter the level of the ski. Simply put, your skis are not receiving the attention to detail that they require for excellent performance. It is an assumption by nearly all major manufactures that their race skis will get ground at a qualifying race shop before being pushed to their potential.
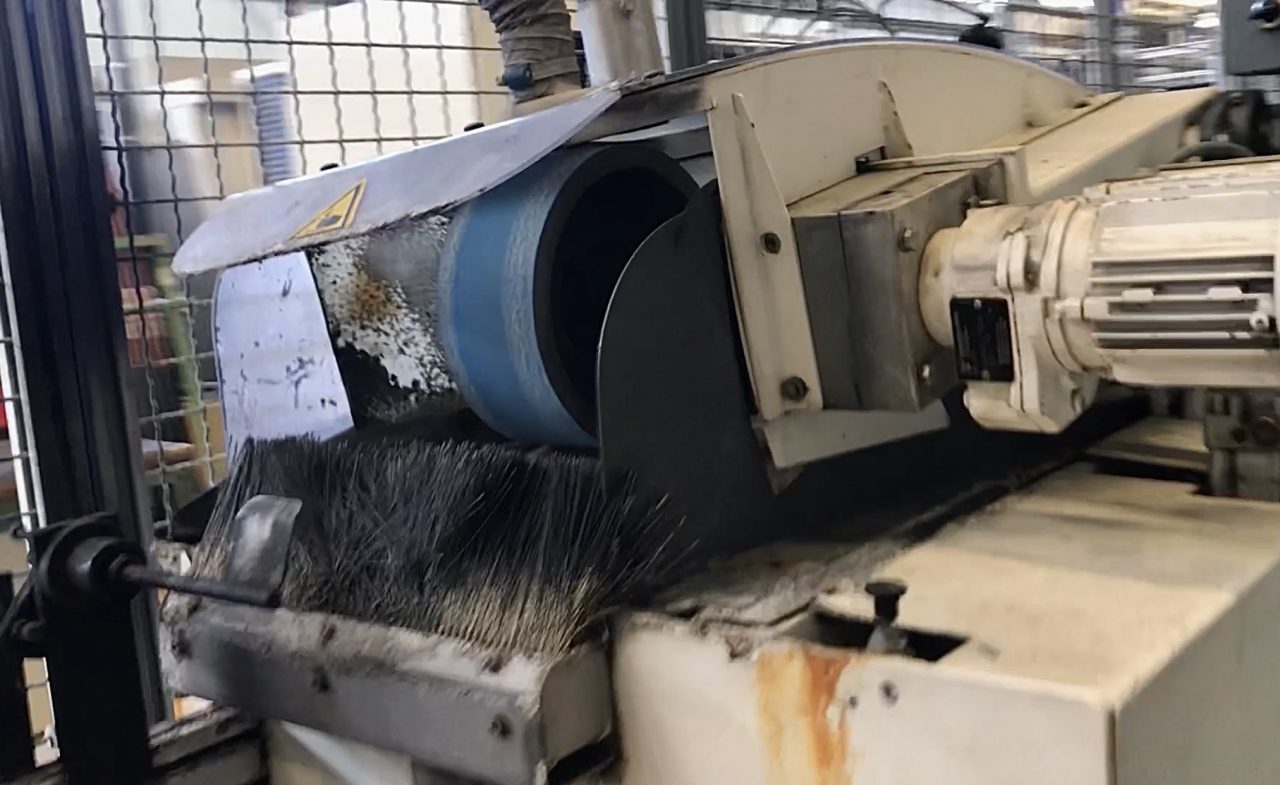
Old/Spare base material is not cleaned out of skis when they are produced and initially ground at the factory. The stone on a stonegrinder is course and porous and spins thousands of times a minute. Over time base material is collected where skis interact and are cut on the stone. As more skis are continually passed some of this excess base material is pressed into the brand new skis. The skis are then sprayed or rolled with paraffin wax as a protectant and shipped out to shops all over the world. This keeps the skis safe during transport but also seals in the loose base material that was not removed. We can remove some of this with a thorough cleaning and brushing at the shop, but a majority gets reheated into the base and diminishes the depth and clarity of your grind.
The stonegrinding process also creates an incredible amount of heat due to friction as skis are repeatedly passed over the stone. This has a smearing effect on the base material as opposed to making a clean and crisp cut. Cross country ski base material is extremely soft and finicky compared to an Alpine ski, so all of these factors compound and make a big impact on the way your skis perform.
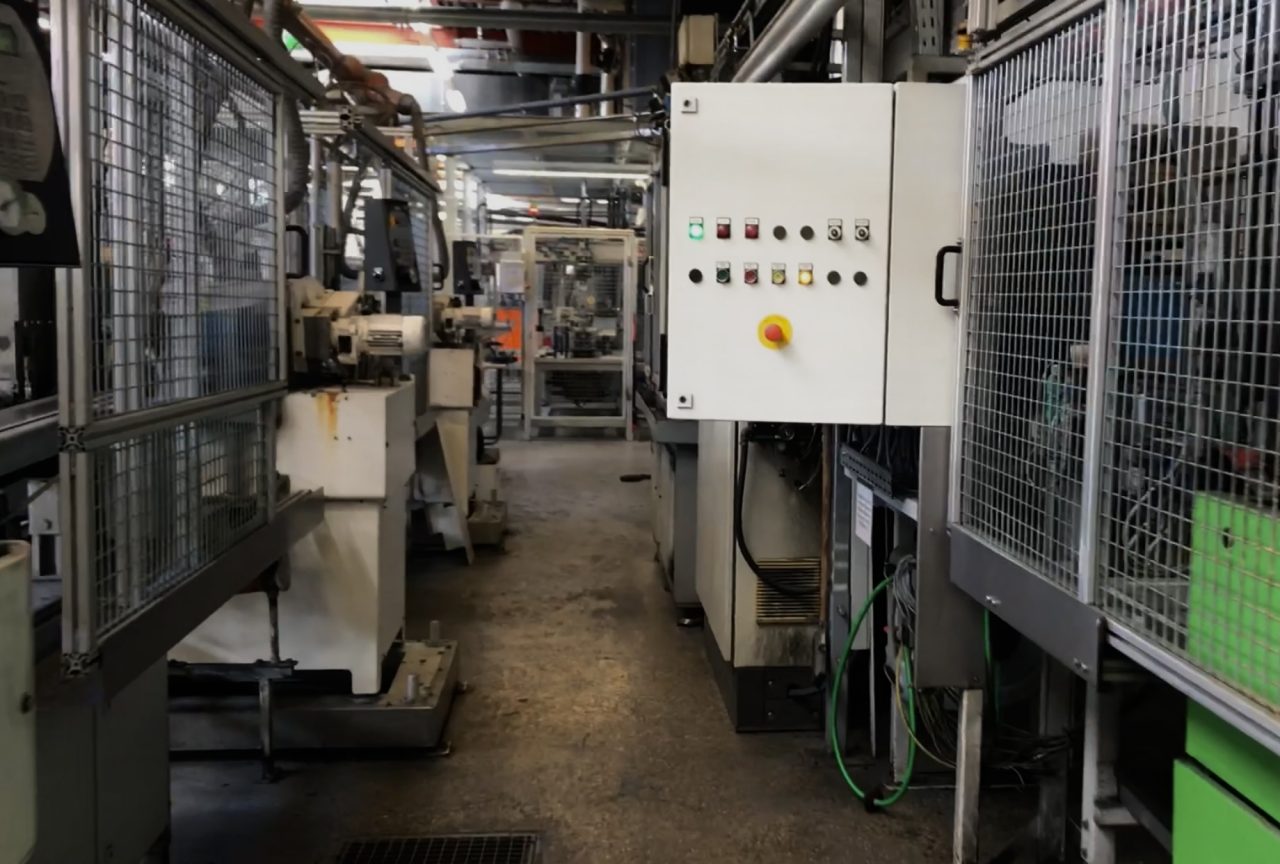
In the past, we have had the ability to get some skis ground specifically for customers one by one on a separate factory machine, but we have found that our in-house grinds have offered more universal performance based on many hours of testing and comparison.
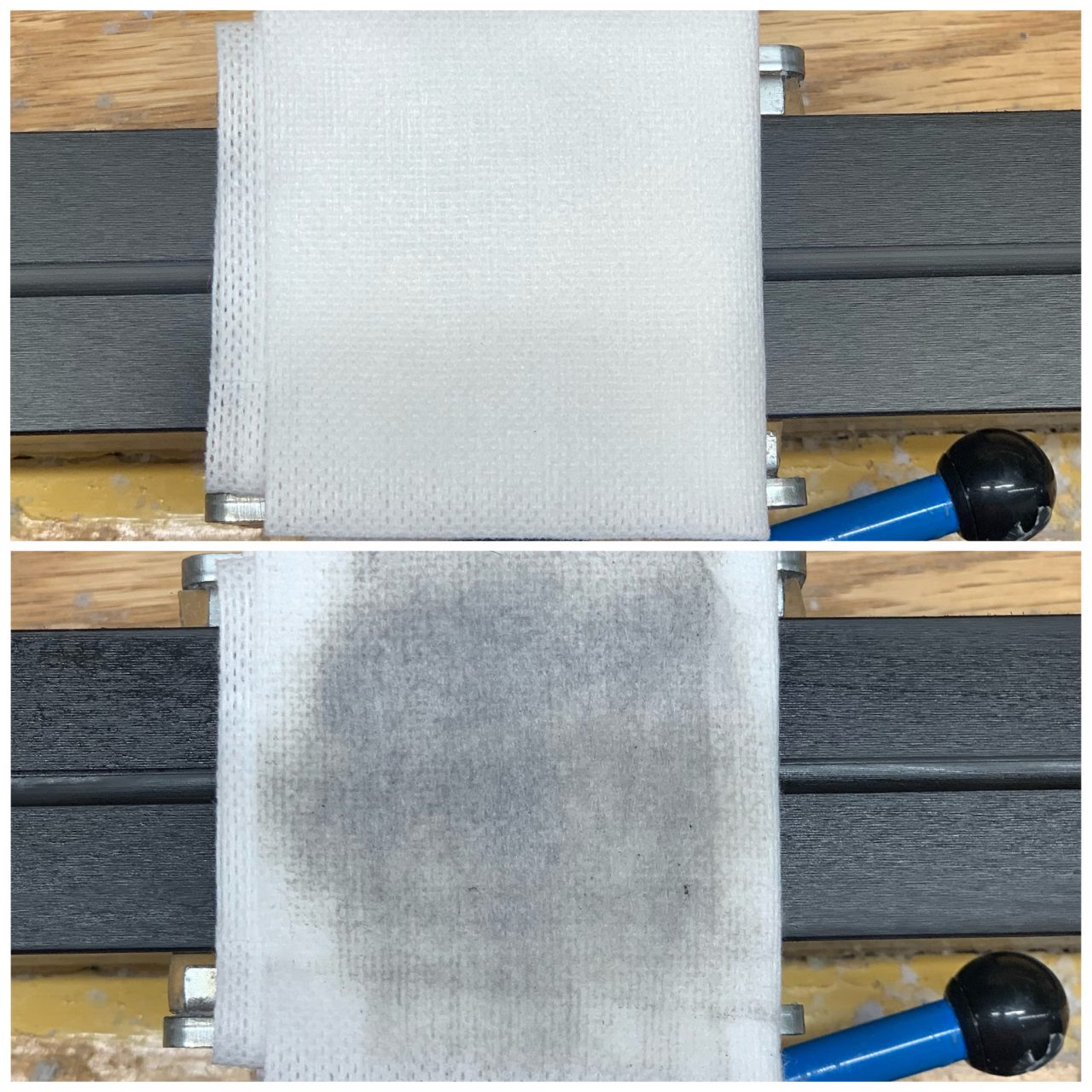
The process of grinding here at Pioneer is broken down into a handful of steps that we constantly test and tweak as new products and waxing regulations hit the market. Each of these steps has been tested by controlling each variable across multiple different structures and snow conditions. Here is a very basic breakdown of our grinding process step by step.
- Pre-grind ski cleaning
- Flattening the ski with a course structure
- Polishing the base material with a very fine/polished stone
- Cutting a new ski grind structure into the ski
- Thoroughly drying and removal of grinding emulsion (low friction liquid ran in our Tazzari)
- Deep cleaning and brushing of the base material
- Running a specific cycle in our Tazzari Thermo Box with specifically developed hotbox wax unavailable elsewhere
- Removal of hotbox wax
- Application of specifically developed race hardening wax for storage and shipping protection

The Tazzari RP23 at Pioneer Midwest is paired with an industrial chiller to control the emulsion to a specific temperature where we can achieve the cleanest cut. We take into account any heat created by friction and have worked to develop grinds that cut cleanly and consistently. Throughout the post grind process, we are using very specific tools and waxing supplies to draw out spare base material and help you get the most out of your grind. The more/cleaner surface area we can expose during the cleaning process, the better your wax will adhere throughout the life of your grind. This process also allows us to analyze our work at each step and make sure we are cutting the highest quality structures.
Stay tuned for future blogs on-base consistency and density as well as deeper dives into the grinding and testing process!